Imagine running a marathon blindfolded—pretty risky, right? Now picture running your building operations the same way, relying on guesswork to fix equipment before it breaks down. Fortunately, AI-powered predictive maintenance is here to rip off that blindfold and light the path ahead, using data and foresight to keep everything running smoothly.
Welcome to the Future of Facility Management
AI-driven predictive maintenance is revolutionizing how commercial buildings operate, allowing managers to spot trouble before it knocks on the door. Historically, this tech has been the shiny toy of large facilities, with big budgets to spend on advanced Building Automation Systems (BAS). But here’s the good news: times have changed. Small to medium-sized commercial buildings no longer have to sit on the sidelines, wishing they could afford this maintenance wizardry. Predictive maintenance is now more accessible, scalable, and affordable for every building, regardless of size
This article explores the specific hurdles smaller buildings face and explains how they can leverage AI and predictive maintenance to boost efficiency, save money, and future-proof their operations.
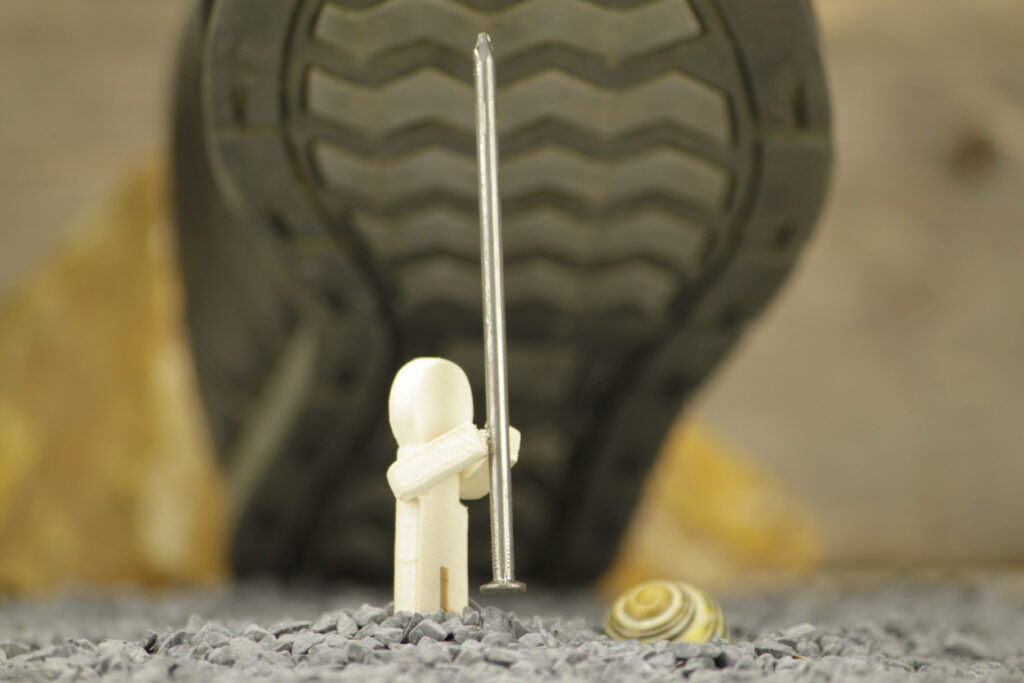
The David vs. Goliath Challenge: Small Buildings’ Struggles
Let’s face it—smaller buildings have always been the underdogs compared to their larger counterparts. With constrained budgets, limited staff, and aging infrastructure, they often resemble David going up against Goliath in the world of building automation. But while Goliath might toss around multi-million-dollar upgrades, David can get smart with predictive maintenance tech that doesn’t break the bank.
Here are the common challenges for smaller buildings:
- Budget Constraints
Large facilities often have deep pockets to install sophisticated BAS systems, but for smaller buildings, convincing ownership to sign off on costly tech upgrades can feel like pulling teeth. They often rely on basic HVAC controls and manual maintenance. Getting AI into the mix might seem like a distant dream. - Lack of In-House Expertise
Big buildings tend to have full teams of engineers and IT specialists who can handle advanced tech. But in smaller operations? Maybe there’s a property manager juggling half a dozen other responsibilities. That person might not have the bandwidth—or the technical know-how—to implement and maintain a predictive system. - Aging Infrastructure
Many small commercial buildings are working with outdated systems from a time when “cloud computing” was just a weather forecast. Retrofitting these older systems to work with modern IoT sensors and cloud-based AI seems impossible without a major overhaul.
Thankfully, there’s good news on the horizon. Recent advancements in cloud technology and AI-driven solutions are bringing predictive maintenance within reach for smaller buildings. It’s not just for skyscrapers anymore.
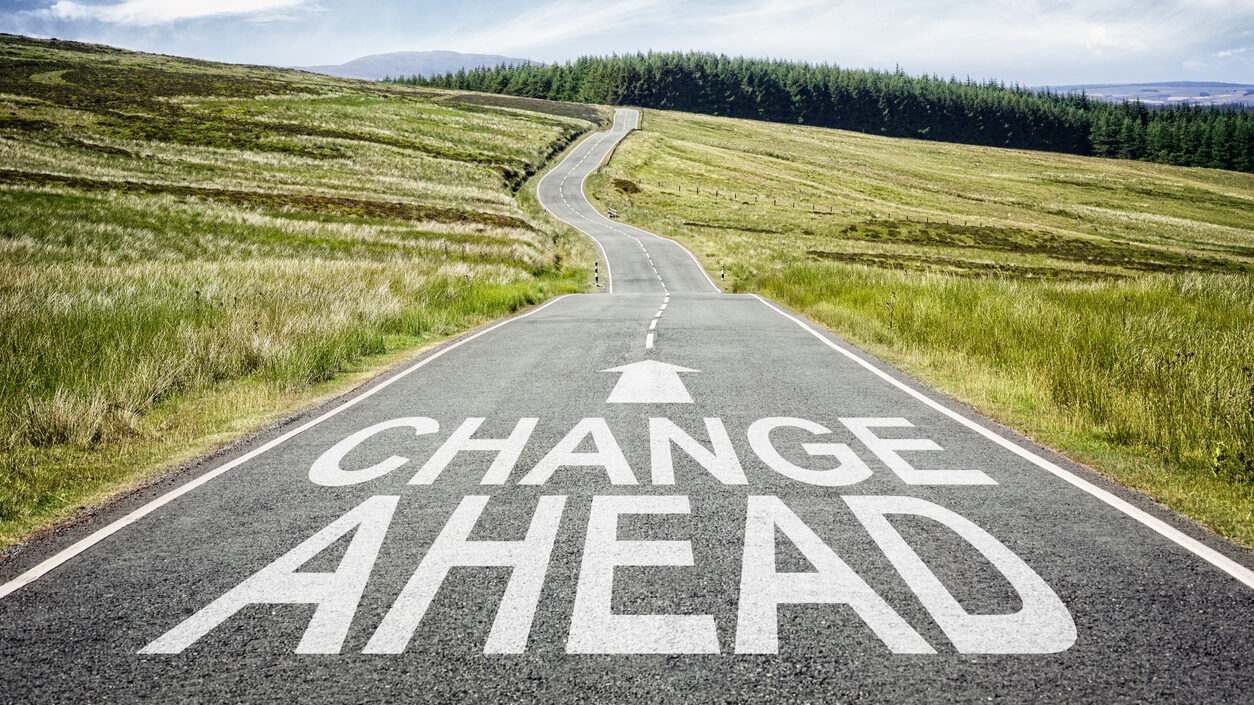
A New Dawn: Opportunities for Small to Medium Commercial Buildings
Predictive maintenance has undergone its own tech glow-up. Thanks to cloud-based systems and affordable IoT sensors, small and medium-sized buildings can now adopt predictive maintenance without taking out a second mortgage. The key? Scalability. Modern solutions are modular, letting you start small and grow over time—no need for a massive upfront investment. Dip your toe in, and see the benefits before diving in headfirst.
- Cost-Effective Retrofit Solutions
Gone are the days when you needed to gut your building to install a predictive maintenance system. Today, companies offer IoT sensors that can be retrofitted onto existing HVAC units, boilers, and electrical systems with minimal hassle. Thanks to edge computing, data processing happens on-site, reducing the need for heavy-duty cloud infrastructure. Vendors now offer subscription-based services, allowing smaller operations to pay only for what they use—no need for an expensive on-prem setup. - Efficiency on a Shoestring Budget
Predictive maintenance helps avoid unexpected breakdowns and keeps operations running smoothly. For small buildings, preventing an HVAC meltdown in the middle of summer isn’t just a convenience—it’s survival. AI constantly monitors equipment and gives early warnings on wear and tear, preventing costly system failures. Plus, it can spot energy inefficiencies, helping you trim utility bills and boost overall efficiency. - Data: The Great Equalizer
It doesn’t matter if your building runs 10 sensors or 10,000—AI doesn’t play favorites. Even a modest setup can deliver insights into equipment performance. Your HVAC unit might look fine, but AI might detect inefficiencies, tipping you off to schedule a tune-up before it becomes a full-blown crisis. It’s like having a mechanic who can see the future, helping you manage your building like a pro, even with minimal staff.
Case Study: The Power of Early Detection
Consider this example: a medium-sized office building installed IoT sensors on its aging HVAC system and signed up for a cloud-based predictive maintenance platform. Within a few months, the system flagged a performance issue in one unit. Instead of waiting for the system to crash, the manager replaced a minor component, avoiding a $50,000 repair bill and days of downtime. Talk about ROI.
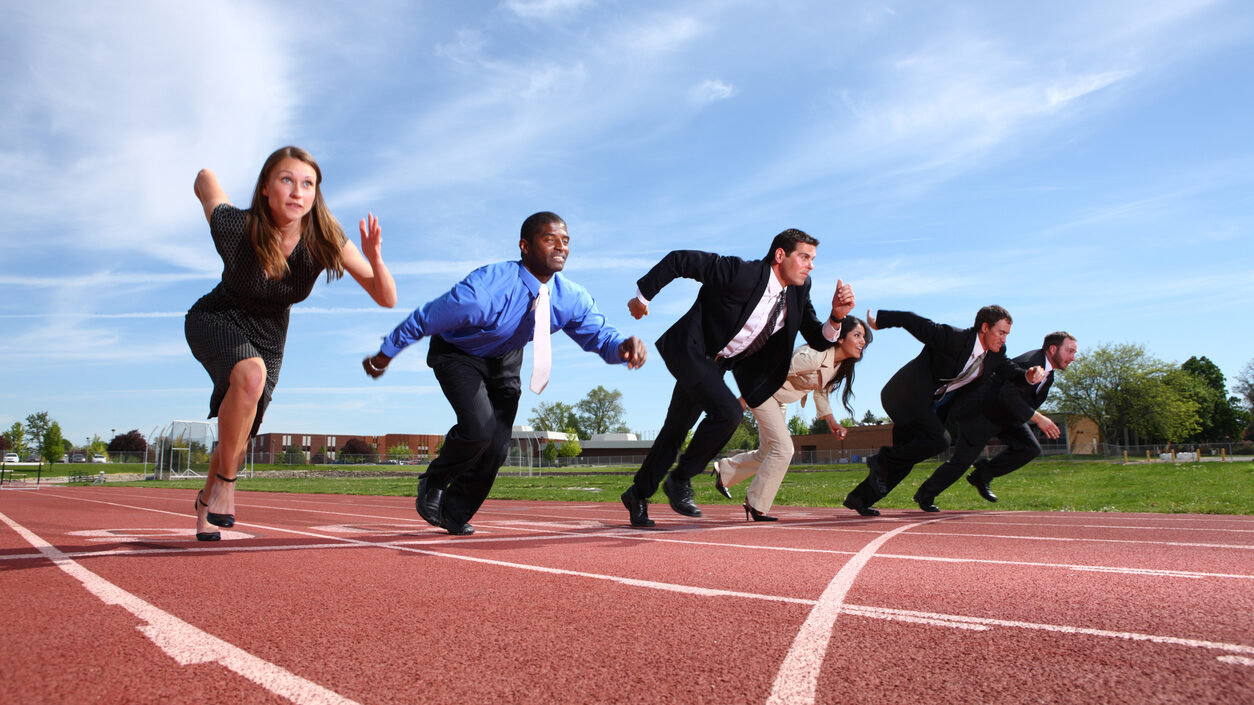
Ready, Set, Optimize: How to Get Started
So, how do you go from zero to AI hero? The trick is to start small, think smart, and scale up. Here’s your game plan:
- Assess Your Current Setup
Identify the critical systems in your building—like HVAC, boilers, and electrical systems—that would benefit the most from predictive maintenance. Even if your equipment is older, IoT sensors can usually be retrofitted, allowing you to collect the data needed to make smarter decisions. - Start Small and Scale Gradually
No need to cover your entire building with sensors from day one. Start with one system, like your HVAC, and see how it performs. Once you notice savings and efficiency improvements, you can expand to other systems. - Find the Right Partner
Look for vendors that specialize in cloud-based solutions tailored to smaller buildings. The solutions should be easy to install, with ongoing support and training. If your team isn’t tech-savvy, make sure the vendor offers strong customer service and guidance. - Monitor, Learn, and Scale
Once your system is up and running, keep an eye on the data. Use those insights to fine-tune your maintenance schedule and optimize energy use. As you become more comfortable, expand the system to cover more areas, gradually turning your building into a well-oiled machine.
Conclusion: Time to Level Up
For years, small to medium-sized buildings have been left out in the cold when it comes to cutting-edge tech. But now, AI-powered predictive maintenance offers a way for these buildings to join the big leagues—without the big-budget headaches. By starting small and scaling up, even the most budget-conscious facilities can reap the benefits of increased efficiency, reduced operational costs, and fewer disasters. It’s not just about keeping the lights on—it’s about stepping into the future with confidence. Who’s ready to take off the blindfold?